The Importance of Ventilation in Underground Mining
Ventilation is one of the most critical aspects of underground mining. It provides fresh air throughout the mine, eliminating contaminants like dust, diesel exhaust, and gases released during blasting. These contaminants pose significant health risks to workers and can create dangerous conditions if not properly managed.
Mines rely on a complex network of ventilation ducts and fans to distribute air. Powerful fans push fresh air from the surface into the mine, while secondary fans strategically direct airflow to necessary areas. The aim is to maintain a constant flow of clean air, ensuring all parts of the mine are adequately ventilated.
However, managing this system is challenging. Mines often allocate 25% to 40% of their energy resources to power ventilation systems. Optimizing these processes is vital to reduce costs and improve efficiency. Additionally, strict regulations mandate minimum airflow rates to ensure worker safety. For instance, Quebec’s mining health and safety regulations require underground mines to supply fresh air at a minimum rate of 15 m³ (529.7 ft³) per minute for each worker underground.
Challenges of Traditional Ventilation Management
Traditionally, underground ventilation management has been a labor-intensive process. Technicians manually measure airflow at various points, requiring physical descent into the mine. These measurements, conducted weekly, must be repeated whenever ventilation system changes occur. The collected data is compiled into reports to ensure compliance with safety standards.
This manual process is time-consuming and prone to inefficiencies. Mines often over-ventilate to compensate for potential air leaks in the extensive duct network. While this approach ensures safety standards are met, it results in excessive energy consumption and higher operational costs. Furthermore, reliance on manual measurements limits the ability to respond swiftly to changes, as ventilation network issues are sometimes hard to detect visually.
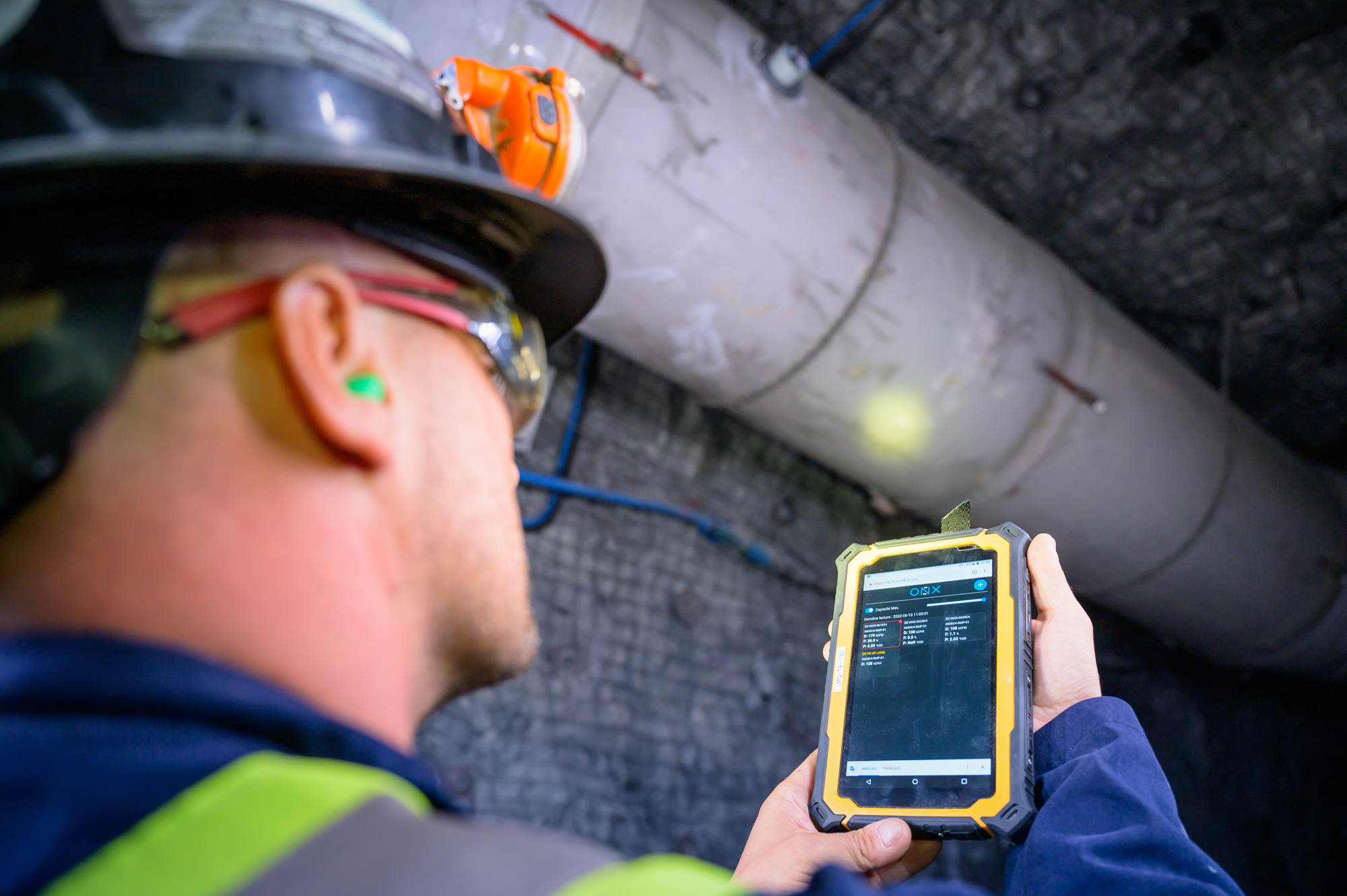
The VORTEN Project: A New Era in Ventilation Management
Recognizing the need for a more efficient and responsive ventilation management system, ONX Automation developed the VORTEN project. This innovative solution leverages modern technologies to automate underground ventilation monitoring and management, reducing manual intervention and enabling real-time data collection.
The VORTEN system includes several key components:
- Wireless Data Sensors: These sensors continuously collect data on ventilation conditions, including airflow and pressure. Their wireless nature allows for easy installation and scalability, as they can be placed throughout the mine.
- Data Analytics Software: Advanced algorithms analyze collected data to detect anomalies (e.g., leaks, fan malfunctions, inadequate ventilation management). Accessible via a web application, this software enables mining operators to monitor ventilation conditions remotely on computers or mobile devices.
- Ventilation Survey Application: Developed in collaboration with Lamaque Mine, this application accelerates on-site measurements, allowing technicians to record ventilation data directly underground. It works with or without a network and centralizes ventilation data for faster report generation.
- Automated Fan Control: Based on data analysis, the VORTEN system can automatically adjust ventilation (e.g., recalibrating based on end-line flow, adjusting backup fan ratios, or fan strength based on leaks) to optimize airflow, reduce energy consumption, and maintain safe working conditions. This automation is a significant advancement over traditional manual systems.
- Rigid Duct Adapters: Installed in ventilation ducts, these adapters are equipped with sensors that monitor air pressure and gas levels.
Project Implementation and Phases
The VORTEN project is structured into eight phases, each designed to gradually develop and deploy the system in a real mining environment:
- Project Initiation: Planning, scoping, and establishing partnerships with key stakeholders like Eldorado Gold, Mécanicad, Lynkz, and Innovscan.
- Sensor Integration: Installing sensors in ventilation ducts to monitor air pressure and detect potential fluctuations.
- Motorized Damper Integration: Installing motorized dampers in ventilation ducts to control airflow. These dampers can be automatically adjusted based on real-time data.
- VORTEN System Deployment: Deploying the complete system, including all sensors, transmitters, and control systems.
- Deployment Environment Optimization: Refining the system to enhance performance and reliability through hardware, software, or network adjustments.
- Real-World Testing: Testing the VORTEN system in Lamaque Mine’s real mining environment to validate its effectiveness and identify areas for improvement.
- Knowledge Dissemination: Sharing project results with the broader mining community through reports, industry conference presentations, and client engagement to demonstrate the VORTEN system’s benefits.
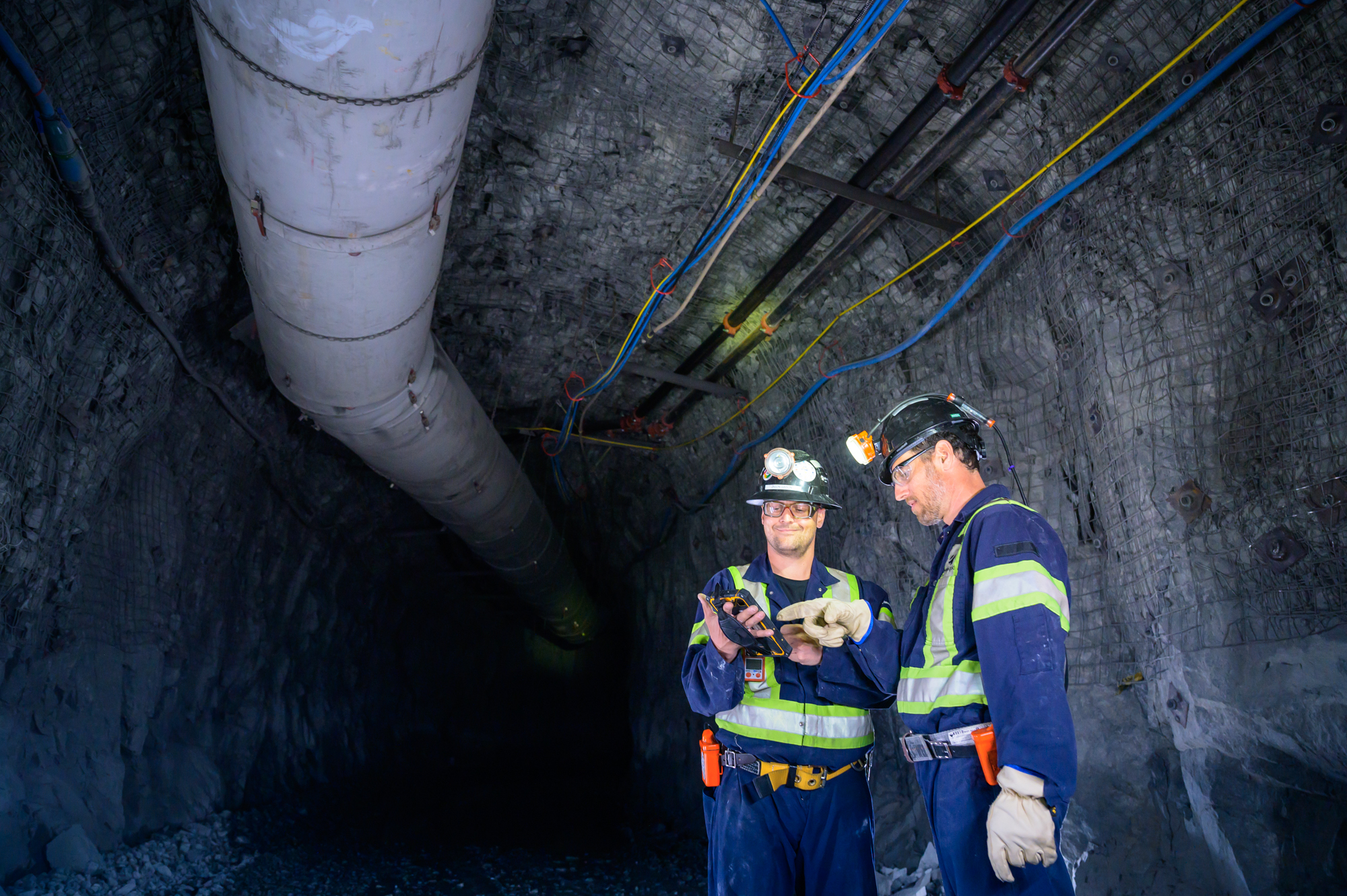
Advantages of the VORTEN System
- Energy Consumption Reduction: Optimizing fan operation and calibrating ventilation networks automatically reduces energy requirements, translating into significant cost savings.
- Increased Productivity: Real-time monitoring and automated adjustments allow for quicker responses to environmental changes, minimizing unexpected shutdowns.
- Improved Health and Safety: The VORTEN system ensures consistent airflow delivery to workspaces.
- Enhanced Operational Efficiency: Automated controls and digital measurement tools accelerate field visits and free technicians for critical tasks.
- Scalability and Flexibility: VORTEN’s modular design accommodates various mining operations, from small mines with basic controls to large complexes with advanced ventilation-on-demand systems.
Economic and Environmental Impact
Beyond immediate cost savings and productivity gains, VORTEN demonstrates the economic and technical feasibility of advanced ventilation systems. Its adoption can significantly reduce energy consumption and the mining industry’s carbon footprint, contributing to overall sustainability.
The VORTEN project marks a significant advancement in underground ventilation management. Through cutting-edge technology, ONX Automation addresses inefficiencies and challenges of traditional systems, enhancing safety, reducing costs, and increasing productivity.
ONX’s commitment to innovation and collaboration with industry partners like Eldorado Gold, Mécanicad, and Lynkz underscores the importance of collective efforts in advancing the mining sector. As VORTEN progresses through its phases, its potential to positively impact the industry becomes increasingly evident, showcasing a future where technology and innovation drive safer, more efficient, and more sustainable mining practices.