Automation of Welding Operations on a Mining Complex Construction Site
The mining industry in Quebec is known for its diverse operations within a dynamic and potentially hazardous environment. Welding tasks, in particular, require special attention due to the risks they pose to both operations and the health and safety of miners. These tasks are not always governed by specific standards but rather by universal regulations applicable to similar professions.
Métal Marquis’s project aims to automate welding operations within a mining complex. In collaboration with several partners, Métal Marquis is working to develop an innovative technological solution to enhance the productivity, safety, and quality of welding operations. The project partners include Aviseo, 48E, Creaform, and Explor.ai, each contributing valuable expertise to achieve the project’s goals.
Welding Risks
Metal welding presents numerous risks to operators. Welders are exposed to hazardous metal fumes that can cause both acute and chronic illnesses, as well as severe conditions like cancer caused by ultraviolet rays. Welders also face the risk of electrocution, not only for themselves but also for those nearby. Other dangers include asphyxiation, burns, eye and hearing injuries, electric shocks, and musculoskeletal disorders. These risks vary depending on the welding techniques, the work environment, and the materials used.
Workforce Challenges
The mining industry also faces a shortage of skilled labor. Welder-assemblers are currently in high demand across Canada, a trend expected to continue growing. Since 2010, welders’ salaries have increased by 13% to attract more interest in this profession. Additionally, the welding profession is regulated in several Canadian provinces, including Quebec, requiring apprenticeships or certifications to practice. This shortage of skilled labor presents significant challenges for mining operations, necessitating innovative solutions to bridge this gap and maintain the quality of services rendered.
Compliance and Quality Control Issues
Adherence to current welding standards and procedures is sometimes ineffective, impacting the robustness and viability of completed work. This leads to additional labor requirements, prolonged downtimes, and unexpected stoppages due to welding defects. In Canada, welding engineering follows well-documented procedures, but quality control is often performed post-factum with technically challenging methods. Automating welding procedures ensures compliance with standards and the use of processes that lead to optimal quality interventions. Moreover, this control allows for documenting their compliance at every stage of the work, thereby reducing risks and improving operational efficiency by issuing alerts before proceeding with work, minimizing the extent of corrective actions needed.
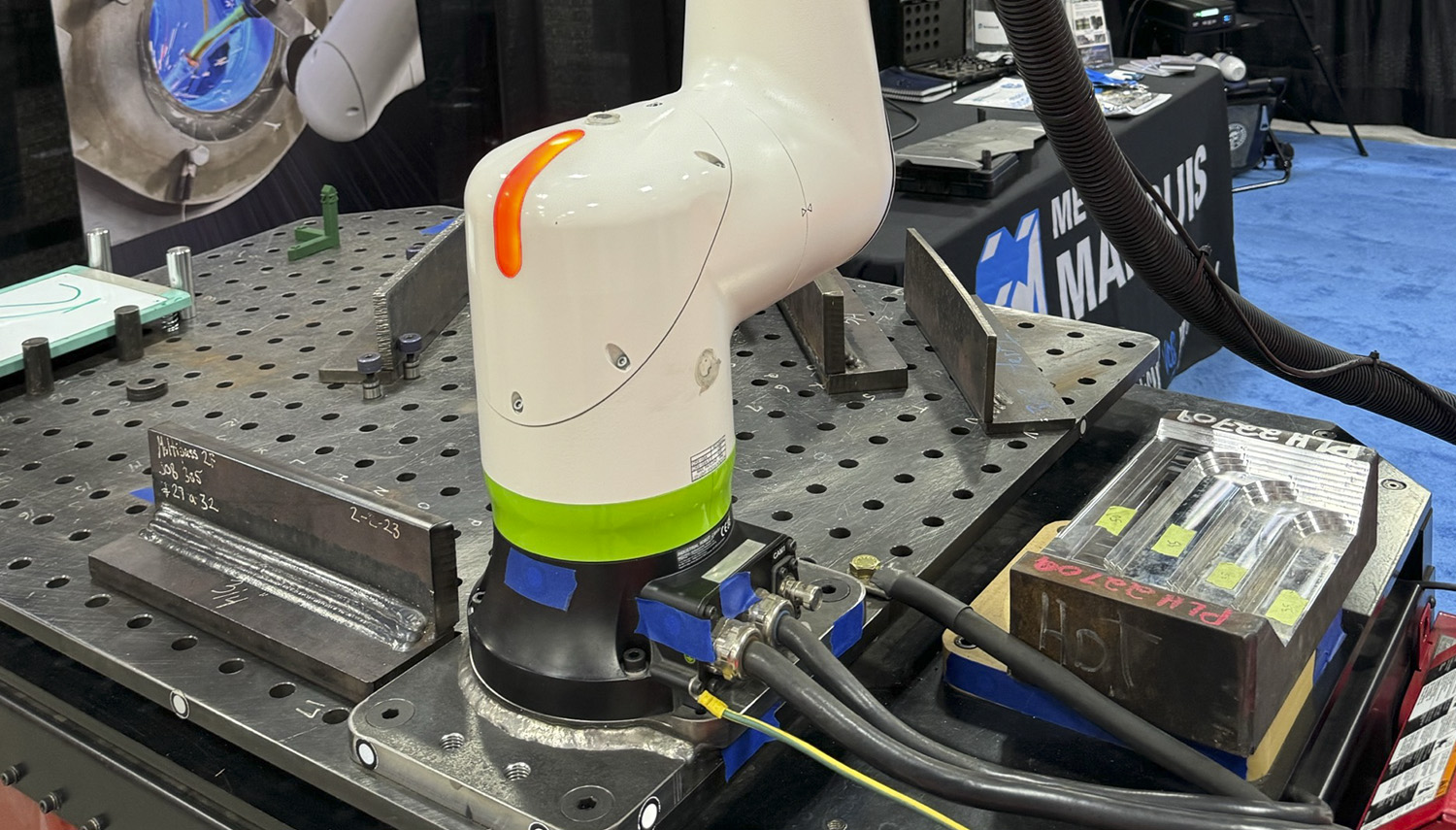
Project Objectives
Aware of the impact of welding work on the productivity of mining complexes, Métal Marquis is developing technology to quickly and optimally deploy a robotic arm in the specific context of mining operations. This robotic arm will perform welding operations under the supervision of an operator, supported remotely by Métal Marquis’s technical team if technical issues arise or specific advice is needed for unconventional welding cases outside the basic procedure library.
The solution proposed by Métal Marquis aims to achieve several key objectives:
- Reduce health and safety risks for welders: By automating certain welding tasks, welders will be less exposed to the inherent dangers of these operations.
- Improve productivity: The robotization of welding operations will increase efficiency and reduce downtimes.
- Ensure regulatory compliance: Métal Marquis’s solution ensures that welding operations consistently comply with standards, regulatory procedures, and best practices.
Real-Time Monitoring and Predictive Maintenance
Data generated by welding operations will be transmitted in real-time to Métal Marquis’s team and stored in a cloud infrastructure for reporting and tracking the progress of work by the maintenance superintendent or other supervisors. This approach will enable continuous monitoring and in-depth analysis of weld performance, facilitating predictive maintenance and proactive intervention planning.
Benefits of Real-Time Monitoring
- Reduction of downtimes: By detecting potential issues before they become critical, real-time monitoring allows for planned maintenance interventions before breakdowns occur, thus reducing unexpected downtimes.
- Enhanced safety: Continuous monitoring quickly detects dangerous conditions and enables immediate corrective actions, improving operational safety.
- Optimization of productivity: By ensuring proactive and planned maintenance, operations can proceed more efficiently, thereby increasing overall productivity by reducing planned stoppages.
Cloud Infrastructure
The use of cloud infrastructure centralizes maintenance data, making it easier for different stakeholders to access and analyze information. This approach offers several advantages:
- Accessibility: Data can be accessed from anywhere, at any time, by authorized team members.
- Security: Data is protected by advanced security measures, ensuring its integrity and confidentiality.
- Scalability: The cloud infrastructure can easily scale to meet the growing needs of the organization, enabling the management of increasingly large volumes of data.
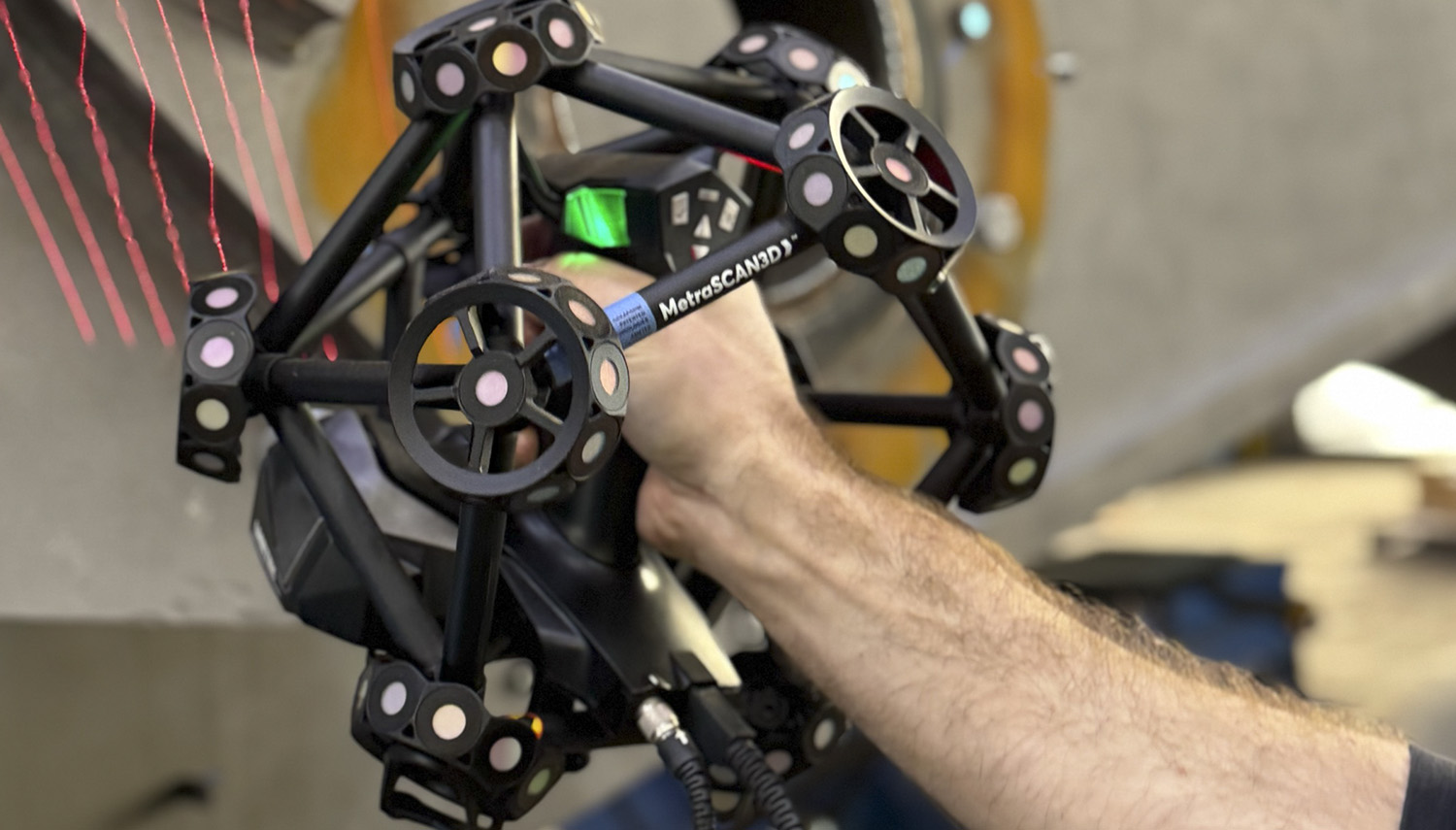
This project represents a significant advancement in the automation of welding operations within the mining industry. By developing an innovative technological solution, Métal Marquis, in collaboration with its partners, aims to open this trade to operators who are not proficient in either welding or robotic programming, thereby addressing the labor shortage while improving the safety and efficiency of welding operations and ensuring compliance with appropriate standards.
This initiative addresses the challenges of skilled labor availability, health and safety risks, and regulatory compliance needs. By automating welding operations and leveraging advanced technologies for real-time monitoring and predictive maintenance, Métal Marquis’s project promises to transform the mining industry towards a safer, more efficient, and more sustainable future.
The success of this project could serve as a model for other industrial sectors facing similar challenges. The adoption of robotic technologies and real-time monitoring could be extended to other types of critical operations, thereby improving safety and productivity in various work environments.
In conclusion, their project is a crucial step towards innovation and continuous improvement in the mining industry, placing the health and safety of workers at the forefront while increasing operational efficiency and maximizing available resources. With the commitment and expertise of Métal Marquis and its partners, this project is well-positioned to succeed and have a lasting impact on the mining sector and beyond.